It is a first in the local pharmaceutical industry – two medications for cardiovascular disease (CVD) manufactured right here in Sri Lanka for the first time, in the market at a significantly lower price for the benefit of patients.
The ‘firsts’ are Cilnidipine and Rivaroxaban from Morison Ltd., part of the Hemas Holdings conglomerate. These medications along with Bisoprolol were launched in Colombo on the theme ‘Touching more hearts’ this Wednesday (February 26).
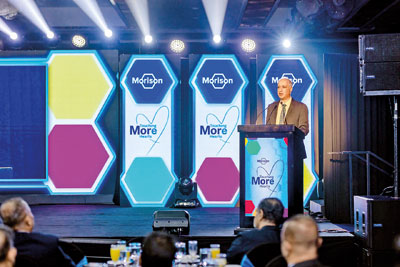
Cilnidipine in the form of 5mg and 10mg tablets, Rivaroxaban as 10mg and 20mg tablets and Bisoprolol as 2.5mg and 5mg tablets have been manufactured at Morison’s state-of-the-art facility at Homagama.
All duly approved and registered with the National Medicines Regulatory Authority (NMRA), Cilnidipine is a 4th generation calcium channel blocker for hypertension (high blood pressure); Rivaroxaban, a direct factor Xa inhibitor anticoagulant; and Bisoprolol, a cardio-selective beta blocker.
These medications would help fight CVD, an umbrella term for conditions affecting the heart or blood vessels. ‘Calcium channel blockers’ stop plaque-forming calcium from entering the cells of the heart and arteries; ‘direct factor Xa inhibitors’ are blood thinners that prevent blood clots; and ‘cardio-selective beta blockers’ are a medication used in the treatment of hypertension, heart failure, arrhythmias (irregular or abnormal heart rhythm) and heart attacks.
“We choose to take the high road,” said the Managing Director of Morison Ltd., Dinesh Athapaththu, stressing that for them it is not just about churning out tablets. “We are conscious that behind every tablet we produce is a person trusting us at their most vulnerable times. Therefore, for us it is not merely a business, but more of a responsibility we take to heart.”
He assured that all their products meet all pharmacopoeia standards and stringent quality testing, as quality is non-negotiable. This is while the price is well below market rates.
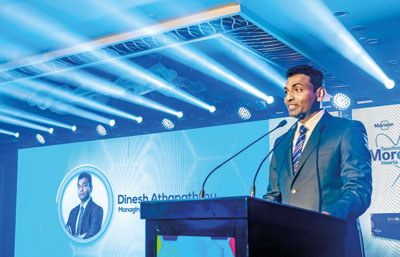
The pricing strategy has the potential to save patients up to Rs. 30,000 or more per year, it was disclosed, making these critical medications more accessible to Sri Lankans.
Looking at the pharmaceutical market share, Mr. Athapaththu said that the government has 40% and the private sector the balance 60%. However, regrettably there was only 5% of the private sector share manufactured by local industry, while everything else was imported.
Expressing “excitement” over what is in the research and development ‘pipeline’ of Morison, the Chairperson of Hemas Holdings, Husein Esufally, went back in time to 1948 when his grandfather established the overall business. It was based on strong standards of governance, quality, safety and efficacy on par with international standards.
He called for stronger links between the government and the local pharmaceutical industry as they hope to stick around for the long haul. “We want to do this for Sri Lanka and this is why we need a stable policy environment.”
Earlier, Morison Ltd., had introduced the diabetes-combating medication Empagliflozin in the form of 10mg and 25mg tablets, becoming the market leader in this arena within two years of its introduction.
The launch was concluded with a panel discussion on non-communicable diseases (NCDs) including heart disease, hypertension and diabetes. The discussion was moderated by Senior Professor T.P. Weerarathna, Dean, Faculty of Medicine, University of Ruhuna, while the panellists were Senior Consultant Cardiologist Dr. Naomali Amarasena and Consultant Endocrinologist Dr. Manilka Sumanatilleke.
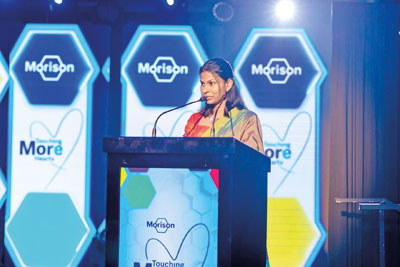
The “major” burden of NCDs and their toll on healthcare costs, lives and suffering were discussed at length.
Disturbing data that NCDs are the 2nd highest cause of hospital admissions and the leading cause of death in the hospital setting highlighted the need for urgent measures and medications to combat this spectre.
More worries came with disclosures by Dr. Sumanatilleke that Southeast Asia is the ‘hotspot’ for diabetes, while in
Sri Lanka, 21% (1 in 5) of the urban adult population is diabetic and another 20% is in the pre-diabetic stage.
He said that it was also concerning that half of these people did not even know that they were in danger, underscoring the need to ramp up screening and identification, followed by treatment.
The panel focused on how 4th generation calcium channel blockers had a different mode of action to older generation medications, which seemed to help minimize side-effects.
Rigorous testing
The MD of Morison Ltd., Dinesh Athapaththu, outlined to the Sunday Times the rigorous tests used by his company to ensure the quality of drugs as per pharmacopoeia
They include:
- Assay – to measure the exact amount of API (Active Pharmaceutical Ingredient) in the product to confirm its strength.
- Dissolution – to test how quickly and completely the drug dissolves in liquid, indicating how it will be released in the body.
- Impurities or related substances – to check for unwanted or harmful substances that might be present alongside the main drug.
Mr. Athapaththu said that in addition they also conduct three micro tests to ensure the medications are free of harmful bacteria and fungi. They are:
- Uniformity of Content (UOC) – to confirm that each tablet has the same amount of API, ensuring consistent dosing. (The test is conducted only if the API% is less than 25% of the total tablet weight).
- WIP (Work-in-Progress) Physical Parameters – three tests to check for moisture (loss on drying), tapped density and bulk density.
- FG (Finished Goods) Physical Parameters – over eight tests to check appearance, weight, friability, hardness, thickness, diameter, metal contamination and empty pockets/broken tablets.
- Meanwhile, three more tests are performed on identification, disintegration and water content, he added